Mold Growth & the Importance of Proper Sequencing During a Construction Project
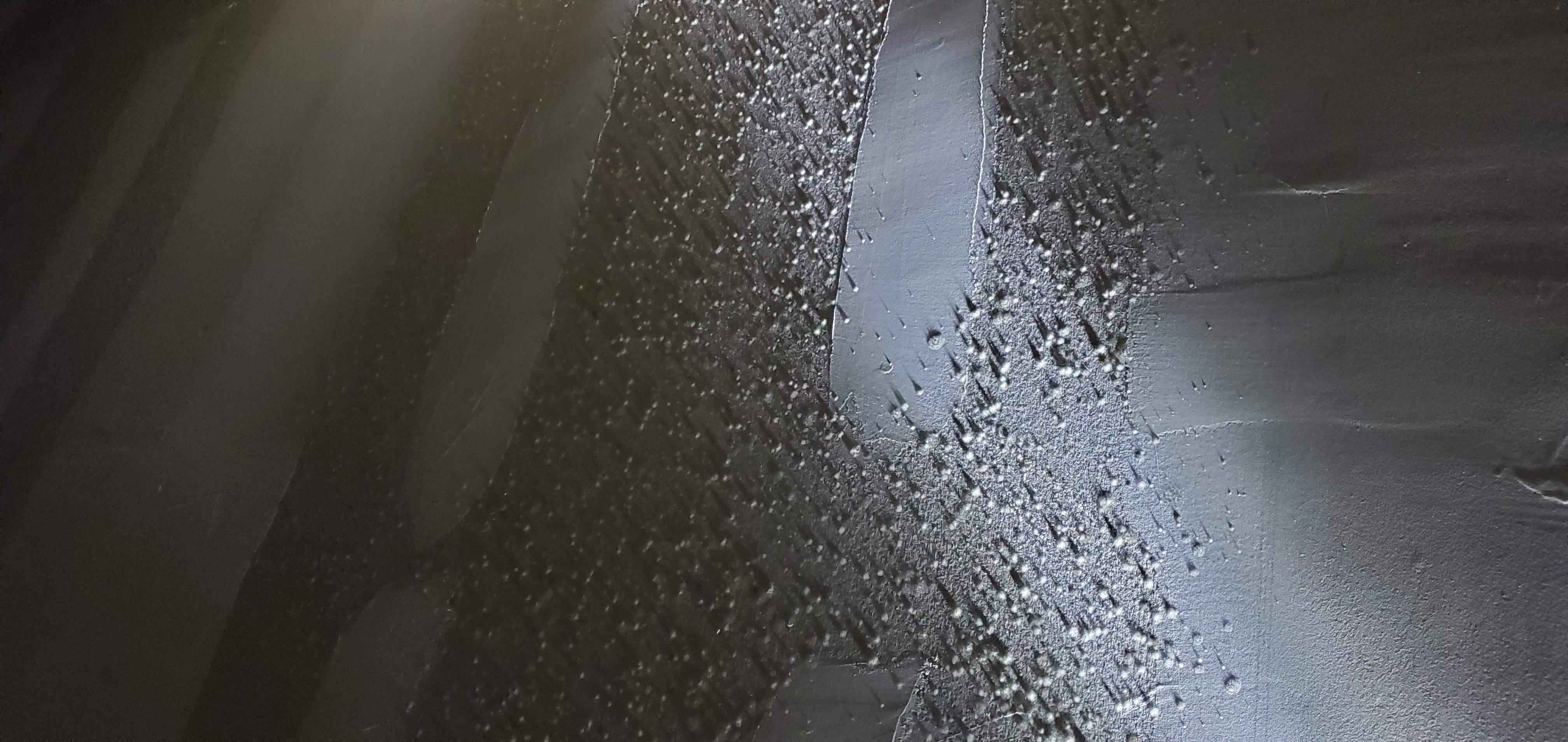
Recently OCCU-TEC, Inc. was presented with a unique project that originated from a seemingly insignificant event- a slight change in the sequencing of construction.
During a major construction project, the general contractor initiated a change in the construction sequencing that caused a significant problem. A problem that inflated the cost substantially, delayed the schedule and caused a rush to purchase materials during a time when materials are expensive and accompanied by significant delivery delays.
The following is a brief outline of the project:
A construction company contacted OCCU-TEC, Inc. to investigate suspected visible mold growth (VMG) on newly installed drywall at a construction site. The facility under construction was large and consisted of several open auditorium spaces and ancillary classrooms.
Upon arrival, OCCU-TEC noted significant condensation on the concrete floor throughout the building. Additionally, suspect visible mold growth could be seen on drywall in several locations throughout the building. After discussions with the general contractor, it was determined that the building's heating, ventilation, and air conditioning (HVAC) units had been installed but were not operational at the time. A sizable amount of drywall had already been installed throughout the building, and recent rains had contributed to elevated humidity levels within the space. Additionally, the drywall installation had occurred during the part of the year where precipitation and humidity are at their highest.
OCCU-TEC observed that the drywall, having been installed before the HVAC systems were operational, had been impacted by elevated humidity throughout the building. HVAC systems in buildings such as this serve to condition the air and prevent elevated humidity. OCCU-TEC determined that the drywall was installed before the HVAC commissioning in order to meet a very tight project schedule.
Although this may not present a problem during certain times of the year, i.e., Winter and peak Summer conditions, the unfortunate timing of the installation during increased precipitation, and the nonfunctioning HVAC units had allowed for increased humidity that facilitated mold growth on drywall surfaces.
OCCU-TEC worked with the general contractor and a qualified mold remediation contractor to develop a Scope of Work to reduce the humidity, remove mold contaminated drywall, and thoroughly clean the building. The plan included using numerous dehumidification units throughout the building and forced air blowers to facilitate humidity reduction and drying. The general contractor had the HVAC units commissioned to condition the air space and maintain a consistent temperature. The remediation contractor removed any drywall that exhibited signs of mold growth. After completion of remediation, all HVAC units were cleaned with an anti-microbial solution. OCCU-TEC provided expert oversight and continued project support to ensure the remediation was completed within the scope designed and in a timely manner to meet the client's requested timeline and expedite the return of other trades to the construction site.
Lastly, OCCU-TEC collected numerous air samples through the project to continuously gauge the effectiveness of the remediation effort and to provide documentation of remediation completion prior to allowing the project to move forward.
In this instance, if the general contractor had sequenced the commissioning of the HVAC units prior to the installation of drywall, the space would have been properly conditioned, and the elevated humidity would most likely not have occurred. This would have saved a substantial amount of money and time for the project.
Needing assistance with project management?